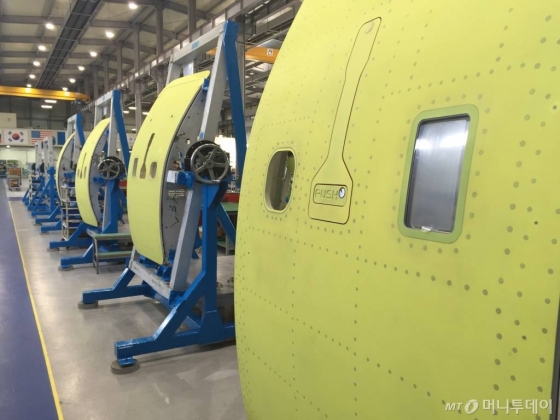
13일 경남 사천 사남면 소재 샘코 (2,015원 ▲105 +5.5%) 공장에서 만난 정 부사장은 "항공기 부품은 언제 어디서 누가 작업했는지 사고가 났을 때 확인이 가능하도록 추적 관리가 필수적으로 이뤄진다"며 "거의 모든 제품을 수작업에 가깝게 생산하고 있다"고 말했다.
샘코 주력제품인 항공기 출입문 1개가 견뎌야 하는 압력은 21톤이 넘는다. 이 때문에 부품 조립에 일반 제조산업군의 10~100배 이상의 정밀도를 요구한다. 운항고도 기준 내외부 압력 차가 5배 이상 발생하는 비행기 특성상 항공기 도어는 0.001인치의 오차도 허용하지 않는다.
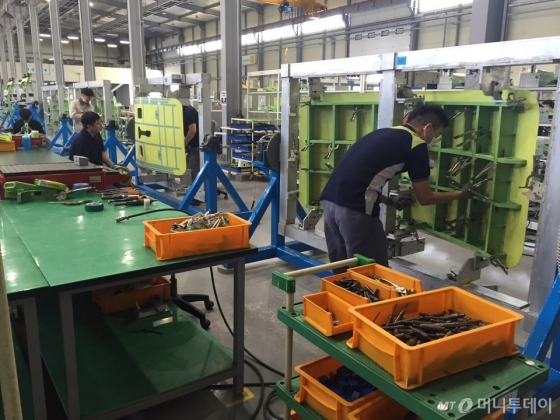
실수가 용납되지 않는 현장 특성상 각 공정의 선임 작업자들은 최소 7~10년 현장 경험이 있는 숙련 인력이다. 볼트, 너트 또는 리벳으로만 연결해야 하는 항공기 도어 특성상 스킨 하나에 800~900개 구멍을 뚫어야 하는데 이 과정은 자체개발한 자동화 로봇이 맡는다.
바로 옆 조립공정에선 보잉 B737·777에 장착되는 슬라이딩도어가 제작되고 있다. 승객용 도어와 달리 항공기 한 대당 단 1개만 장착되는 슬라이딩도어는 조종사 등이 비상 탈출할 때만 이용하는 문이다. 개당 단가가 6000~8000달러인 슬라이딩도어는 월 40~50개가 생산된다.
이 시각 인기 뉴스
정 부사장은 "슬라이딩도어의 알루미늄 부품을 외부에서 생산하다가 샘코가 직접 주물·성형까지 담당하면서 공급 원가를 20% 절감했다"고 설명했다.
샘코는 항공기 부품 성형·가공부터 도색·조립·검수까지 90% 이상 제작공정을 자체적으로 수직계열화했다. 조립공정이 주를 이루는 1공장 바로 옆에는 알루미늄 원판을 성형·가공하는 2공장이 있다. 성형 공장은 정확도가 중요한 만큼 거의 모든 장비가 자동화돼 있다. 작업자 한 명이 장비 세 대를 동시에 다룬다.
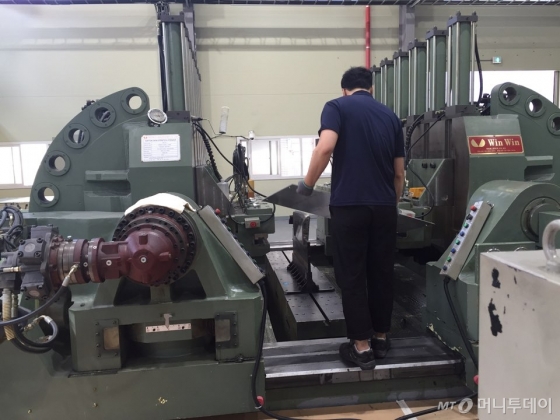
성형과 단면 마감을 마친 알루미늄은 냉장고에 보관된다. 혹시나 열이 가해질 경우 모양이 틀어지는 경우를 방지하기 위해서다. 이후 녹 방지 등 특수공정이 더해지고 도색에 들어간다. 또 모든 알루미늄 성형물은 조립 공정에 넘어가기 전에 공차 오차를 점검하는 과정을 거친다.
내달 준공 예정인 1만8000㎡ 규모 산청공장에는 40억원에 발주한 1000톤 스킨 스트레쳐가 들어간다. 이 장비는 러시아·중국업체들과 논의 중인 150인승, 250인승 등 대형 기종 도어를 제작하는데 사용될 예정이다.
샘코는 내년 하반기까지 산청공장에 표면처리공정을 구축해 외주비율을 낮추고 자동화 설비를 늘려 원가절감에 나설 계획이다.
회사는 산청공장에 공모자금을 포함 150억원을 투자할 계획이다. 신규 투자 비용의 24%는 중앙정부·경상남도·산청군 예산에서 되돌려 받는다. 샘코가 향후 현지 인력을 45명 이상 고용한다는 조건이다. 샘코는 올해 경상남도 소재 기업 중 첫 상장 기업이기도 하다.
이창우 샘코 회장은 "수주 이력이 쌓이자 국내외에서 생산능력(CAPA) 이상의 주문이 밀려들어 일부 고객사에서 제안하는 일감은 거절할 수밖에 없는 상황"이라고 말했다. 그는 "중소기업으로선 드물게 에어버스, 수호이 등 대형 고객사의 신뢰를 얻는 데 성공했지만 끊임없는 원가 절감 노력만이 이들 고객사를 유지하고 성장해 나갈 수 있는 방법"이라고 덧붙였다.
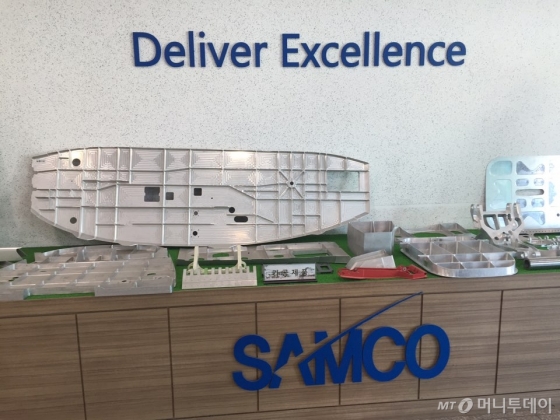