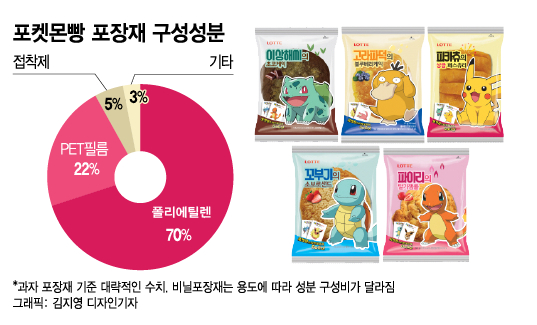
비닐은 PE(폴리에틸렌), PET(페트) 등으로 이뤄진 석유화학 물질이다. 지금까지 비닐쓰레기는 태우고 땅에 묻는 것 말곤 별다른 처리 방법이 없었다. 하지만 이젠 달라졌다. 포켓몬빵 봉지와 같은 비닐쓰레기에서 석유를 뽑아내는 기술이 나왔다. 이른바 '플라스틱 유전'을 가능케 한 열분해유 기술이다. 폐플라스틱 열분해유 공정으로 석유화학제품을 만들면 폐플라스틱을 태우는 방식에 비해 2배 이상 온실가스 감축 효과가 있는 것으로 나타났다.
이렇게 나온 열분해유를 곧바로 석유화학 공정에 투입할 수는 없다. 열분해유는 불순물이 많이 섞인 탓에 설비를 망가뜨리고 제품 불량을 불러올 수 있다. 공정 투입을 위한 후처리를 거치면 열분해유의 95% 수준의 공정 투입용 열분해유를 만들 수 있다. 열분해유 600㎏를 가정할때 570㎏ 정도다.
김태진 SK이노베이션 환경기술연구센터장은 "열분해유 반응기를 끄지 않고 열처리를 이어가면 궁극적으로는 투입하는 폐비닐 양의 80%까지 열분해유를 만들 수 있을 것"이라며 "폐플라스틱은 지역이나 계절, 환경 등에 따라 불순물 등 상태가 달라지는데 이를 석유화학 공정 요구 스펙에 얼마나 적합하게 맞추는 지가 연구의 관건"이라고 했다.
'탄소중립 치트키' 열분해유
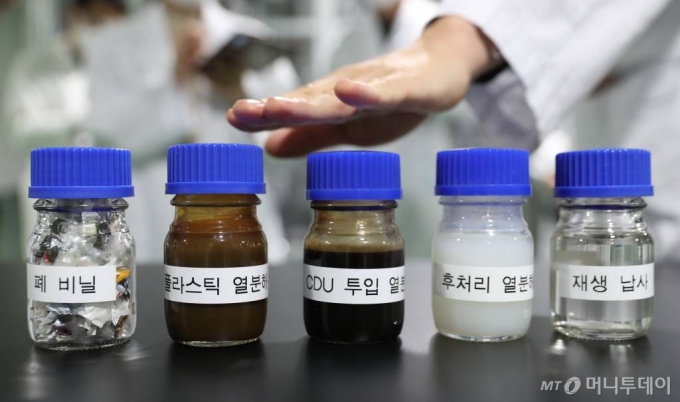
이 시각 인기 뉴스
비용만 놓고 보면 열분해유를 만들어 투입하는 것은 기존 석유화학 공정보다 오히려 비싸다. 폐플라스틱에 열을 가하고, 불순물을 제거하는 과정에서 기체로 사라지는 성분 손실과 에너지 손실 등은 모두 경제성을 떨어트리는 요인이 된다. 쉽게 말하면 배럴당 100달러를 넘어선 원유라도 열분해유에 비해선 '싼 재료'라는 얘기다.
그럼에도 열분해유 시장이 주목받는 것은 탄소배출 감축 의무와 기업의 환경적·사회적 책무 때문이다. 전 세계적으로 설정된 2050년 탄소중립 목표에 비춰보면 열분해유라는 탄소배출 저감 기술을 무시하기 어렵다.
SK이노베이션이 한국기후변화연구원(KRIC)와 공동개발해 환경부 배출량 인증위원회로부터 승인받은 '폐플라스틱을 활용한 열분해 정제유를 석유정제제품 원료로 사용하는 방법론'에 따르면 폐플라스틱 1톤(t)을 열분해유로 사용할 경우 폐플라스틱을 소각하는 것보다 2톤 이상 이산화탄소가 줄어드는 것으로 나타났다.
현재 폐비닐의 처리방식인 소각에는 가열을 위한 연료와 폐비닐이 타는 과정에서 △이산화탄소(CO₂) △메탄(CH₄) △아산화질소(N₂O) 등 온실가스가 배출된다. 열분해유 공정은 기존 사업에 비해 온실가스를 감축·흡수·제거가 가능한데 폐플라스틱 1톤을 기준으로 비교하면 열분해유 활용이 소각에 최대 2.7톤까지 이산화탄소 감축효과가 있는 것으로 추산됐다.
독일·네덜란드·일본 멈췄던 열분해유 산업 재시동
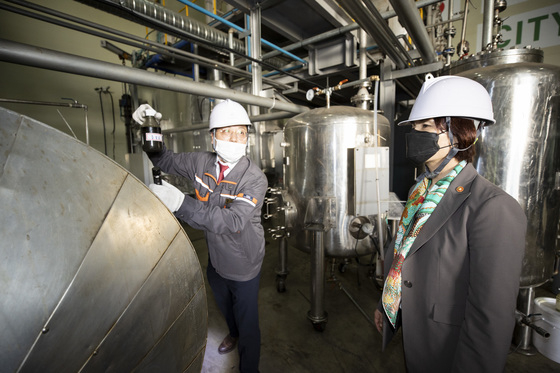
폐플라스틱 열분해유 시장은 1990년대초 일본과 유럽, 미국 등 나라에서 싹트기 시작했다. 당시 기술은 폐플라스틱을 중질유로 만들어 산업용 난방 등에 쓰는 데 초점을 맞췄다. 하지만 폐플라스틱 원료 수급이 어려워지고 열분해유의 열효율이 떨어지는 탓에 2000년대 들어 기술개발과 상업화가 중단됐다.
최근 들어 다시 열리기 시작한 열분해유 시장은 석유화학 제품의 원료와 수소·메탄올 합성 소재 등 열분해유를 통한 고급 소재 개발에 집중돼 있다. 독일의 바스프(BASF)는 2023년 가동예정인 열분해 오일 플랜트를 건설 중이고, 네덜란드의 사빅(SABIC)은 지난해 하루 2만톤의 생산 능력을 갖춘 열분해 오일 플랜트를 만들었다.
일본의 에바라(Ebara-Ube)와 캐나다의 에너켐(Enerkem) 역시 하루 생산량 300톤 규모의 열분해유 시설을 각각 2기, 1기씩 상업운전하고 있다. 이들 기업 모두 기술고도화를 통해 오일과 합성가스 생산수율을 극대화하고 열분해유 정제를 거친 납사(나프타) 생산을 목표로 삼고 있다.
우리 정부도 지난해 말 발표한 'K(한국형)-순환경제 이행 계획'을 통해 2020년 1만1000톤 수준인 열분해유·가스생산량을 2030년까지 연간 90만톤까지 늘리고, 버려지는 폐플라스틱의 열분해 비중을 2020년 0.1%에서 10%로 끌어올릴 계획이다. 이를 위해 지방자치단체와 순환자원유통지원센터, 업계 간 폐플라스틱 공급계약을 체결하고 열분해유 지원금을 신설하는 등 제도적 지원을 추진 중이다.